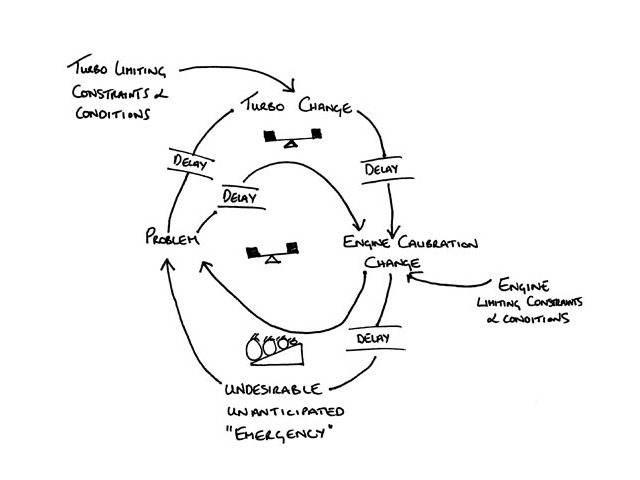
Our online stores are always open to meet your needs.
Diamond Diesel |
Ebay | Amazon
March 18th, 2018 8:49 pm
Written by Dennis Brookshire, Engineering Director, Global LD Product Line & Technology Line Leader – Two-Stage Turbo Systems
"Development of Cummins Turbo Technologies Integrated M2 Two-Stage Architecture using Rotary Turbine Control (RTC) Technology for the Cummins 5.0L V8 Turbo-Diesel Engine." Posted By Dennis Brookshire, Engineering Director,
Cummins Turbo Technologies recently launched a pioneering new Two-Stage turbocharger, the next generation Holset M2 TM Two-Stage System with Rotary Turbine Control (RTC) which is Cummins’ most sophisticated turbocharger to date and delivers high efficiency, excellent driveability and low emissions levels. Successfully developed simultaneously to a major new engine development for Cummins, the ISV 5.0L is a new engine platform for Cummins with its flagship launch on the 2016 Nissan Titan XD pickup truck in North America.
This article is a summary of the paper delivered at the 20th Supercharging Conference and highlights some of the system and product development challenges involved in the development of this fully integrated system, specifically looking at the product development challenges of the RTC system.
System Engineering Challenges
The integrated M2 system differs from the other turbochargers in the market by its unique architecture and also the complexity of packaging the turbocharger. Due to the physical size of this architecture, the turbocharger’s most obvious first challenge was to fit or package it in space whilst avoiding surrounding engine components and optimizing for the many potential risks of being in such close proximity to other important engine sub-systems and components. Along with the highly interactive functional requirements, a system thinking mind-set had to be at the core of every team member to achieve program requirements. The project required a high performance team capable with the skills necessary to solve complex problems where both requirements and capabilities were unclear and fuzzy at the outset of the program. The team members had to have the skill and/or tools available to break down critical complex functions into definable functional objectives to execute the project. The full version highlights a few of the more useful system tools used on the journey.
Product Development Challenges
Nowhere was product development more challenging than in the Rotary Turbine Control (RTC) System, which is a groundbreaking development for the industry. This turbo technology had many new, unique and/or difficult (NUD) functions and components where engineering standard work and traditional computer-aided engineering (CAE) models lacked capability and/or real world usage correlation. This created a greater dependence on the use of a combination of critical thinking, Six Sigma, product and systems engineering tools. The repeating scenario that the team often found themselves in can be best visualized using a Mental Model Archetype as shown in Fig 1.
Rotary Turbine Control (RTC) System
![]() |
The main challenge of this turbocharger development was the RTC system and its many functions required using an actively controlled exhaust-side valve. Figure 2 shows various modes the valve allows. In most if not all conventional automotive sequential two-stage turbo architectures to this point, the state-of-the-art is to use a wastegate style poppet swing valve to achieve the bypassing function between the two turbochargers. For the RTC valve system, it doesn‘t end here. Not only is it utilized to channel (or bypass) flow between two turbines, but it has the additional functional requirements of an integrated wastegate for the low pressure (LP) turbine as well as exhaust throttling functionality to enable engine warm-up and aftertreatment regeneration. These added functions within a single valve design is something not seen in the industry today and represents a significant breakthrough in exhaust-side valve technology.
However, with the added functionality came significant technical challenges:
• Design Packaging Constraints - another NUD for this system was to attach the actuator for the RTC system not on the turbocharger itself, but on the intake manifold cover. This provided easier access to the actuator for serviceability, but introduced design and product development challenges with respect to tolerance stack-up and variation.
• Kinematic Challenges - the RTC control valve with all of its functionality required over 130 degrees of rotation presenting significant kinematic challenges and no fewer than half a dozen design iterations throughout development.
• Reliability - one challenge often seen with actively controlled turbochargers is the ability of the flow control device to operate reliably in a severe non-lubricated, high temperature diesel exhaust gas environment.
• Torque Output - having sufficient torque available at the actuator (i.e. capability or “supply” of torque) vs. the torque required to turn the RTC valve (i.e. mechanical system requirement or “demand” for torque) under all possible scenarios is one of the most challenging elements of developing actively controlled turbocharging systems. Having a positive torque margin is required, therefore solving this challenge involves a delicate blend of design changes to reduce demand whilst ensuring robust supply of torque at all times.
Due to the high degree of system complexity and relative immaturity of advanced computer aided engineering tools, running expensive physical testing often became the most time and cost efficient way to learn about the interactions and product capabilities and iterate on the designs. Developing correlated models was then needed to help drive the validation testing away from hardware toward virtual CAE tools, but often still fell short in capability due to the complex nature of the system.
Outlook for the Future
Developing this fully integrated system brought about many system engineering and product development challenges but the end result is one of the most sophisticated turbochargers that Cummins has developed to date, delivering high performance that enables excellent driveability, low emissions and fuel economy. Cummins Turbo Technologies are confident that we have a product that enables Cummins to achieve many successes in the future on this product. Future variants of this technology are already in exploration and Cummins Turbo Technologies hope to utilize the lessons learned on this program and apply them to future opportunities around the globe. To learn more about the Holset M2 Two-Stage System with RTC and its different modes of operation view our video on YouTube.